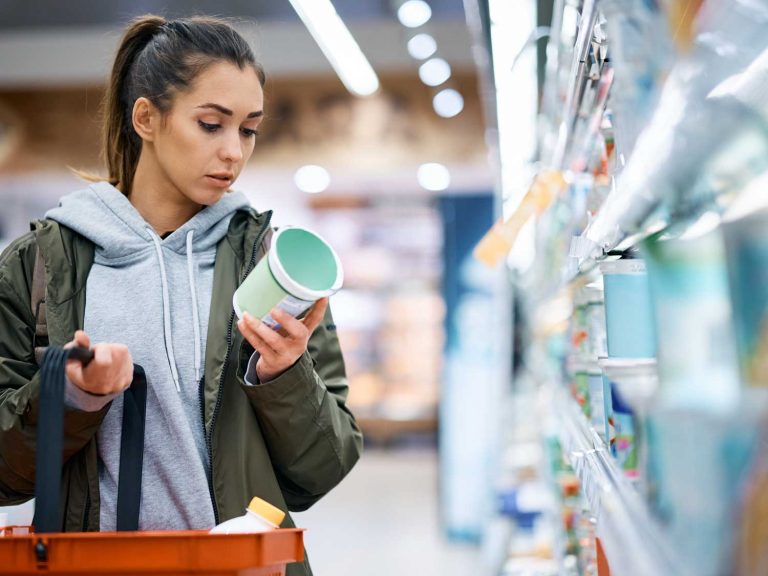
Date:
Visibility in the food supply chain
For many importers, the underlying problem that prevented them from pivoting their supply chain as the pandemic’s impact became more pervasive was lack of visibility and control upstream.
The food supply chain has stabilised since the pandemic, but new macro events continue to create disruption, including the war in Ukraine and the cost of living crisis and where there is a lack of visibility, it prevents the timely, proactive action that optimises operations in the face of disruption.
Participants across the food and drink sector still need that greater transparency and control, to ensure an effective, resilient and flexible supply chain is available, whatever challenges arise.
End-to-end visibility removes uncertainty in the supply chain, by providing the wider business with a view of inventory supply upstream and when they can expect to receive particular product batches.
With clearer visibility and transparency between production, shipping, storage and distribution, it is easier to anticipate any supply shortages or delays, so they can immediately overcome the issue, or update the business, so that alternative sources may be accessed and implications for customers avoided.
Delivering visibility in the food supply chain
This importer of food products and raw materials is a major international manufacturer of branded grocery products, that includes many market-leading household names and consequently has a vast integrated global supply chain, with many layers of complexity.
The supply chain visibility solution that has been developed for them by Metro comprises seven core functions, and a users portal with dashboard, which provides a real-time view of the entire supply chain, together with drill down options for each of the seven functions.
- POMs (Purchase Order management)
- We receive a feed of PO/SKU data, with suppliers confirming quantities, dates and place a booking at origin. Tolerances are set and approvals required for anything outside of certain dates or other values.
- EBSA (E-booking space and allocation)
- Vessels bookings are allocated to POs and carrier contracts.
- Track and Trace with AI powered ETA
- SKU level tracking with market leading predicted dates. Vessel AIS images and automated delay logging – with reasons.
- Report centre
- Key KPI reports such as average days a container is at port, transit and delivery times within SLA agreement, bookings per week by carrier split.
- Bespoke reports also built around financial reporting and inbound forecasting.
- DCM – Distribution centre management for 3rd party DCs
- The DCM has been tailored to their requirements and includes integration with Port Health. Container landing, customs clearance, and released for collection are timed, so client can specify containers for priority, or ‘drill in’ to see the SKUs inside and prioritise collection accordingly.
- My Notifications
- Client is closely monitoring inbound vessel movements based around a strict tolerance.
- MVT Eco
- ECO tool measures emissions and GHG output, by individual shipment, within their supply chain.
EMAIL Simon George, Technical Solutions Director, to learn more.