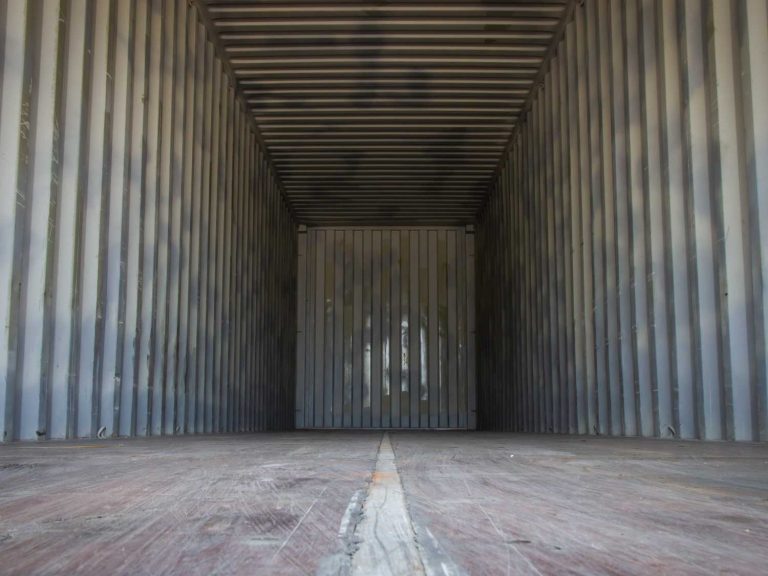
Date:
Dealing with shipping container condensation
Over 200 million shipping containers are transported globally every year, with the vast majority moving through different climate zones, which can create condensation in the container and lead to many kinds of damage.
Considerable temperature fluctuations can occur inside freight containers during transport and storage and since warm air can absorb more moisture than cold air, drops in temperature in closed freight containers may result in the formation of condensation, which can result in corrosion and rusting of steel cargo, mould on packaging and goods, damp packaging and detached labels.
Condensation in containers manifests itself in three primary ways: ‘container rain’; ‘container sweat’; and ‘cargo sweat’, with an estimated 10% of containerised traffic experiencing moisture-related issues.
Container rain is when water on the interior surfaces of the container, concentrates and falls directly onto the cargo, while container sweat usually occurs when container walls cool and cargo sweat usually occurs when air in the container heats up faster than the cargo, with condensation forming on the surface of the packaging.
The amount of condensation in a shipping container varies widely depending on many factors, including container usage, temperature, air space, ventilation, and the moisture content of the goods being shipped.
While it’s impossible to prevent moisture buildup entirely, there are several ways to control condensation, with ventilation and load space critical, because when the difference between internal and external temperatures is small, condensation won’t form as readily and when a container is filled there is less air to hold moisture.
However, if the shipping container is transported in mostly wet and humid conditions, ventilation can pull moist air from the outside and encourage condensation. In these cases we would recommend improving the insulation of the cargo and using desiccants to absorb excess water from the air.
Desiccant bags can be hung from the ceiling and along the walls to help reduce the moisture in the air and make condensation less likely to form on the walls of the container. While desiccant blankets are hung over the goods to prevent condensation from forming and protect products from water droplets and desiccant pads lay below goods (typically liquids) to soak up leaks or extra moisture.
Countering the formation of condensation during container transport depends on a multitude of factors, including the nature of the goods, the climatic zones transited, the size of the container, the weight and moisture content of the goods, the packaging and transport duration.
To a certain extent, shipping container condensation is inevitable, but because we have years of experience keeping containerised goods safe and dry, that doesn’t mean it has to damage your cargo.
Our sea freight team have direct experience in the management of container equipment and work closely with our shipping line partners to ensure that containers are ventilated adequately and that they are free from damage.
If you have questions or concerns on any of the issues raised here, or have specific supply chain challenges, EMAIL Andrew Smith who can advise on the effectiveness of desiccants, humidifiers, alternative packaging and insulation for different types of cargoes and geographies.