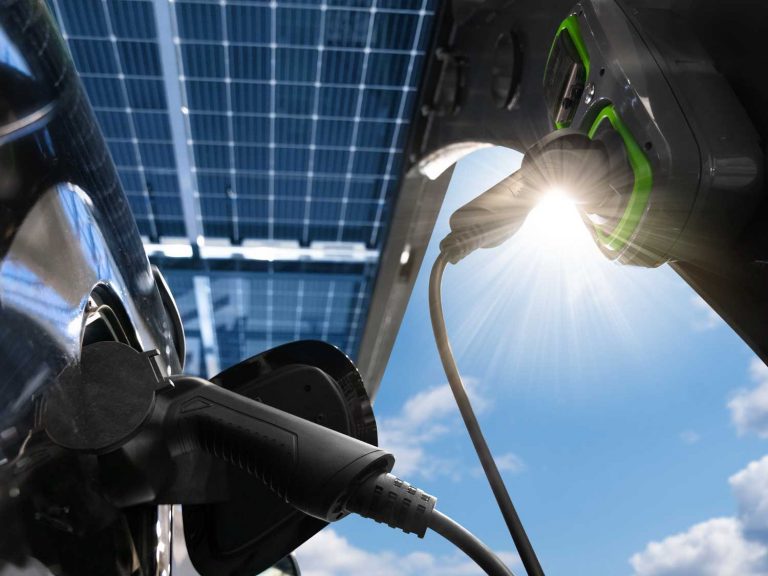
Date:
Automotive trends – We are in lockstep
In a sign of the growing strategic significance of supply chain management for carmakers, two major manufacturers have appointed chief supply chain officers (CSCO) this month. Their appointments come after the industry has battled disruption to production and supply chains, shortages in semiconductors, and supply and logistics cost and capacity challenges.
The Ford and Renault appointments come as automotive manufacturers increasingly put top priority on efficiency, capacity, quality and digitalisation across their supply chains, with UK car sales recovering from their slump in the pandemic and Ford reclaiming the best-seller title.
Keeping up with demand
New car registrations rose by 16.7% in May, the 10th consecutive month of growth as supply continues to improve. Large fleet registrations continued to drive the growth, up by 36.9%, which has been attributed to greater availability following challenging supply issues in 2022.
British car manufacturing continues its resurgence, with output growing 9.9% in the latest monthly figures and exports up 14.7%, with 80% of UK-made cars being exported
UK car production is up 13.1%, driven by uplift in exports, with the EU the largest market, followed by the US, China and Australia.
The global volume challenges of RoRo PCC and PTCT services are well-document in the trade press and are likely to remain a serious challenge for several years.
Metro is supporting exports by shipping cars in containers, with significantly lower port to port freight costs, to avoid the long wait for delayed RoRo services, which have seen freight rates spiral due to congestion and shortage of space.
Standard 40’ containers can accommodate two large cars, properly secured and, with a rack, four small vehicles can be loaded which, with container rates falling to new lows, offers massive efficiency gains and costs that are in line with historic RoRo levels.
Digitalisation
David Leich, executive director of global supply chain at General Motors said last year that those working in supply chain faced up to 200 unique global supply chain disruptions a week impacting the delivery of inbound parts and the delivery of finished vehicles, while only 6% of them have full visibility of those supply chains.
To monitor its supply chain for potential risks that could delay or halt shipments JLR is planning to use a combination of Artificial Intelligence, predictive analytics and machine learning in combination with “human intuition”, to help avoid industrial disruption that could affect production and increase costs.
The introduction of the technology, by JLR and other manufacturers, is part of a wider move to digitally enable supply chains, with end-to-end visibility and security.
Metro is increasing use of predictive and AI technology, to collate real-time carrier updates, to maintain accurate vessel ETA’s, data for purchase order management, route optimisation and supply chain visibility.
We are developing our telematics capability, to offer shippers a much more effective alternative to the data aggregators, who are quite simply compiling data from open APIs and screen scraping historic data. We favour the ‘smart container’ technology that a number of carriers are developing, and are actively involved with UN CEFACT in creating industry standards for sharing this data.
In addition to creating visibility along the supply chain, Metro’s technical solutions team have worked hard to ensure the quality of data and provide a suite of reporting tools that make it easier to interpret and implement actions in a meaningful way.
Lithium Batteries
Growing demand from consumers and government incentives are driving demand for EVs globally and with more EV models coming out from more brands over the next two or three years, the added growth in battery demand means that manufacturers and supply chain infrastructure will struggle to satisfy demand.
Bloomberg Intelligence, told Automotive Logistics that while the semiconductor supply constraints are now beginning to ease, battery supply to meet demand will be the next problem, with potential bottlenecks from 2025 for the supply of lithium batteries into electric vehicle (EV) production.
Metro’s automotive teams handle the movement of thousands of EV’s and battery components every month, by all modes of transport including – when appropriate – the use of refrigerated equipment, to maintain ambient temperature levels, for additional safety precautions.
We started developing our Lithium battery logistics platform over six years ago and since then we have invested in the resource to serve this vertical, including training to cover all modes.
Our Li-ion transportation expertise is increasingly recognised as market-leading, with our automotive team’s manager invited to address the International EV battery conference.
If you would like to learn more about our automotive logistics capability, or to discuss any of the issues raised here handling, please EMAIL Ian Tubbs, Automotive Manager at our Birmingham HQ.