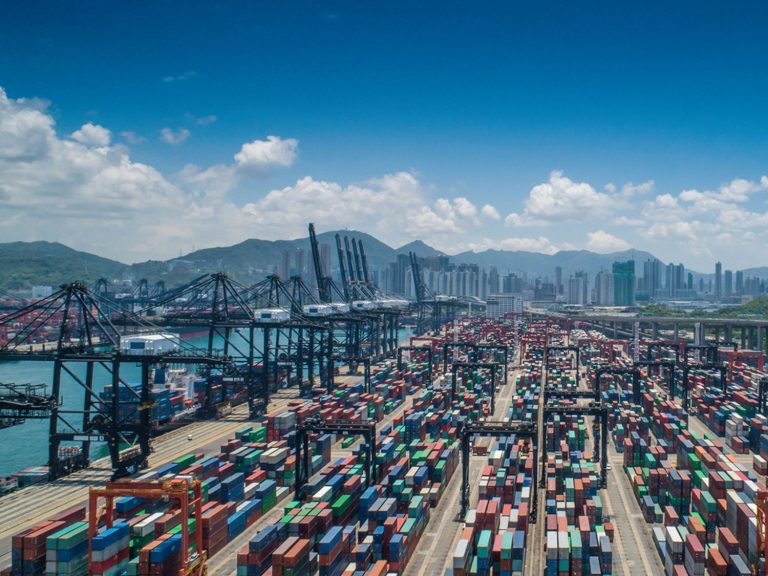
Date:
Q2 sea freight market report
With the 2nd quarter (Q2) of 2021 just a week away, we review five key issues, that are likely to impact maritime logistics platforms over the next three month period and the actions that you can take to protect your cargoes and the integrity of your supply chains.
Equipment, space and congestion issues remain a challenge in many regions. Congestion created delays lead to falls in schedule reliability and increased port omissions while limited moves at busy terminals mean that conditions for roll-overs continue at the busiest transhipment hubs. This could be further accentuated with current events in the Suez Canal as we have updated separately and the temporary closure of the vital lifeline on the East and Westbound container trades.
Against this background of falling reliability and service, shippers – at least in the short term – have to accept the carriers dominance means that high prices and surcharges will continue and will possibly only soften once the shipping lines take positive action to deal with this imbalance.
BAF/Increased fuel costs
As outlined in our accompanying BAF feature – Lines set to impose new round of fuel surcharges – increases in marine fuel costs over the 1st quarter and in particular Very Low Sulphur Fuel Oil (VLSFO), together with expectations of even more demand as lockdowns ease, have provided the background for the shipping lines to increase the level of the Q2 BAF.
The BAF increases will take effect from the 1st April 2021 across all global trades and routes in line with established BAF mechanisms and means that we must also raise our BAF levels to the same line. Confirmation updates will be sent in due course.
Equipment shortages
We have outlined in previous market reports over the last six months how the slower circulation of containers, rather than scarce vessel capacity, has been the most critical issue of the pandemic-challenged supply chain.
The issue is not a shortage of new equipment; last year the industry added about 2.8 million TEU new containers, just exceedingly slow replenishment, because global network disruption and delay means units are out of place.
Simply. Too many empty containers are stranded where they are not needed and not available where they are required to be loaded. This is especially the case at the main Chinese ports and has an impact through the whole of Asia.
The shipping lines had expected the issues to ease during and post Chinese New Year, however, due to continued high export volumes out of the Far East, along with the continued slowdown of operational processes and vessel delays, the challenges being faced are back to the levels that were experienced before Chinese New Year. Many carriers are operating ‘hand to mouth’ with newly arriving empty container inventory being immediately released for loading resulting in an ongoing cycle of shortages across the industry.
To obtain the required equipment, we encourage our customers to share forecasts and book early; two actions that do such to mitigate the challenges being faced.
Forecasting
Due to the current equipment and space shortages in Asia, the shipping lines are now requesting an extended timeline for accepting contracted Far East import bookings, to three weeks.
There are potential financial and service risks associated with bookings made inside the three week window, that can be avoided by longer term booking and forecasts.
We have seen a number of instances, when cargo booked less than three weeks in advance, is either rolled, or removed from ‘contracted volume’ and reassigned to the higher priced ‘FAK’ market.
The more visibility and forecasting we can have, the more chance we have to ensure your space and equipment availability are provided at the contracted rates. We therefore request that going forward with immediate effect you reiterate to your shippers the importance of booking in advance – with a minimum requirement of 21 days prior to cargo ready date. We will discuss this with you in greater detail as we will need to adapt our processes to accommodate going forward.
Vessel Schedules
Container vessel schedule reliability, remains at an all-time global low of 35%, which is the lowest KPI on record, resulting in delayed vessels and blanked sailings, as the shipping lines try to get loops back on schedule by missing out port calls or whole sailings.
Blanked and missed sailings mean that space then becomes an issue due to a high number of roll over bookings. It also means that the replenishment of empty equipment from surplus areas to deficit areas slows down, which exacerbates the already difficult situation in areas like the Far East.
As reported by Metro previously, these challenges affect both the main haul and back haul trades, import sailings and exports. Carriers continue to use every available container vessel they can, and are taking actions to get their services back on schedule, which will assist an improvement in both equipment availability, port delays, and space issues.
UK Haulage and multimodal first/final mile movement
The lowest ever vessel schedule reliability, together with port omissions and other changes – often at the very latest point – is massively impacting the capability and reliability of line haulage.
Large container vessels frequently arrive at ports on different loops and alliances at the same time, creating massive peaks at the new arrival port and troughs at the intended arrival port.
This results in the constant rescheduling of booked line haulage, rail connections and feeder ships when the vessel is delayed, or does not arrive as planned.
At Metro, we also offer a more reliable merchant haulage option, which allows greater flexibility for our customers and suppliers, so we can overcome the uncertainty of late schedule changes and the supply and demand issues that that follow. This can include swap and drop of static containers through to early movement to inland container depot or local railhead. We have options that are under the hourly management of Simon Balfe and his dedicated transport task team.
The increased quality of this service does attract a modest premium, plus a lift on lift off charge for a merchant haulage solution, but the enhanced flexibility and reliability this delivery option offers, adds a lot more value and certainty to our customers supply chain and delivery planning.
In Summary we foresee continued disruption and challenges across the sector which continue to be influenced by known industry issues as detailed, but also by decisions of consumers and the resultant demand, of government legislation and actions and other unforeseen situations which are occurring (as we have seen this week with the Suez canal closure) and metro will continue to manage your container logistics and your expectations in line with the realities of the market.
For further advice please contact with Grant Liddell to arrange a full review and quartley meeting with the full team of stakeholders – we are eager to continue to share daily developments and our flexible and agile solutions to combat the changing environment and ensure the best option is always provided!