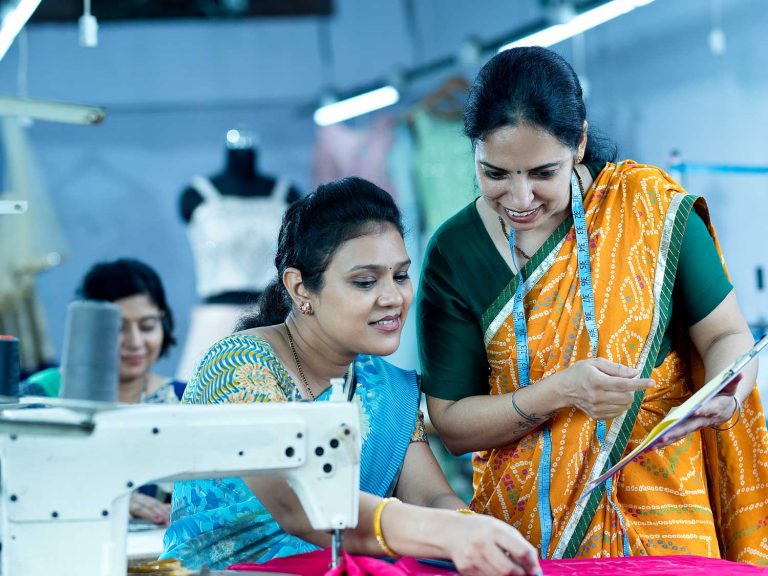
Date:
Sourcing insight; Buyers strategically moving production from China to India
Post-pandemic globalisation is not dead, but as China’s zero-COVID strategy continues it is evolving, as buyers reassess China sourcing risks and diversification and the alternative production capacity that India offers is badly needed, particularly given that Vietnam and much of Southeast Asia are hitting their limits.
As widely reported in the international media this week, new COVID outbreaks are creating further lockdowns in China and this quote from The Loadstar outlines the logistics impact, as of yesterday.
‘’Lockdowns in key Chinese port cities are again hampering supply chains, despite a “muted” peak season and President Xi gave no indication of a change to China’s zero-COVID policy at the Communist Party Congress this week, where he is expected to obtain a record third five-year term in office.
Indeed, in what has now become a regular occurrence, COVID restrictions are impacting supply chains in Ningbo, Shanghai, and Tianjin. Ningbo is the worst affected, with forwarders reporting disruption to the area around the port going into lockdown.’’
Apple has already moved 5% of its iPhone 14 production to India and US importers are increasing their sourcing from the country, with inbound shipments from India rising over 12% in 2022, though this growth is eclipsed by the UK’s goods imports from India, which grew by over 50%.
Apple has been manufacturing iPhones in the southern Indian state of Tamil Nadu since 2017 and by 2025, analysts expect a quarter of all iPhones to be produced in India, as trade tensions between Beijing and Washington show no signs of letting up.
Over 5% of the UK’s importers – >14,000 – are already importing from India and the number is likely to grow exponentially, as many companies looking to “de-risk” global supply chains are looking at alternative supply sources, because of political uncertainty and China’s “zero-Covid” policy.
China’s zero-COVID strategy for eradicating the pandemic has already led to factory closures and large-scale supply chain disruption, with buyers increasingly adopting a “China plus one” strategy, or avoiding the country entirely and re-engineering their supply chains.
The trend towards dual and omni-sourcing is clearly good news for emerging manufacturing power-houses like India, Vietnam, Turkey and Mexico.
Metro’s footprint in India continues to grow, to meet our customers demand, with our expanding team of 50 relocating to a much larger, custom-built, facility in Chennai next year, driven in part by the government’s commitment to building manufacturing capability.
Prime Minister Modi’s government is offering financial incentives to companies that are keen on making India their production hub, which is attracting foreign investment in sectors such as manufacturing and electronics, including semi-conductors, which are critical components for many of our customers.
Encouraged by these production-linked incentives a renowned mining conglomerate is investing £17bn to set up a semiconductor plant in India in collaboration with the Taiwanese electronics manufacturing giant Foxconn, taking India a step closer to its own ‘Silicon Valley’.
The ascendancy of India as a sourcing region, mirrors near-shoring activity closer to home and in particular within the EU, sub-Saharan Africa and Turkey, where we have integrated transport networks, designed to support JIT manufacturing requirements.
These transport networks are ideally positioned to support new sourcing requirements, de-risking and simplifying a critical strategic decision.