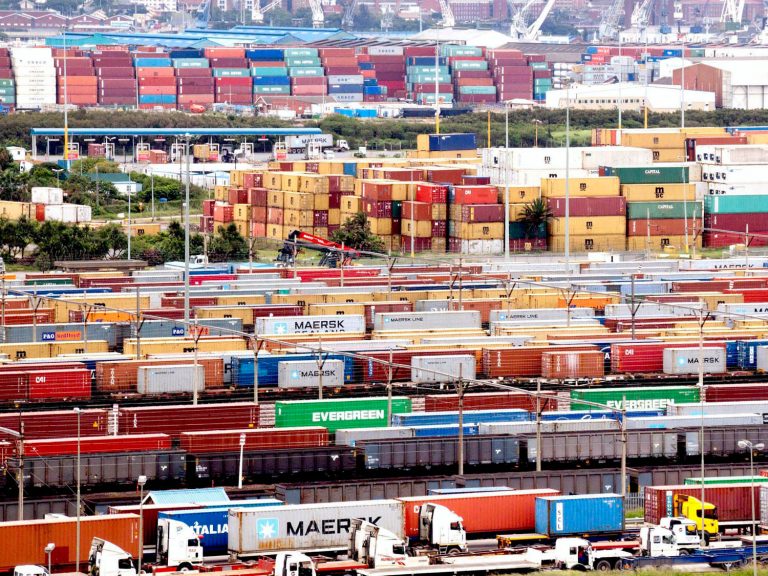
Date:
Why some supply chains fail in the current environment
Brexit and the COVID pandemic has put global supply chains, and the people who work in them, into the public consciousness for probably the first time. As disruptions impact supplies of consumer goods, leaving empty shelves and fears grow for Christmas stock availability, people are asking ‘what’s gone wrong’.
Supply chains almost never operate perfectly. There’s too many processes, participants and ‘spinning plates’, to throw a spanner in the works. The reality is supply chains have always had issues, but freight forwarders put them right and because the thing consumers wanted always turned up, no one was really paying attention. That is part of the value we have traditionally added to the global movement of your products – making issues logistics invisible so that you can get on with your own core business functions.
Weather, economics, capacity, pricing, labour disputes, strikes, regulatory changes and accidents are just some of the issues impacting trade and overcoming them is part of managing cargo flows for forwarder and supply chain executives. But the pandemic and its after-effects are much more profound. Why is that?
The simple answer is that the sudden, unexpected and massive surge of demand that followed the lifting of lockdowns, far exceeds the market’s capacity and ability to cope with the consequences. Supply versus demand dynamics were, and continue, to not be matched.
The existing global supply chain infrastructure simply can’t handle the volume of products flowing through the economy, as consumer demand shifted from purchasing services to purchasing physical products.
For another insight on this critical subject we recommend you view this excellent report on ‘Global supply disruption’ by the BBC journalist Ros Atkins – WATCH VIDEO – it gives a simple but comprehensive overview of what has and is happening in The UK and globally within the logistics arena.
With inventory limited, by domestic and global production shut downs, businesses pushed hard for more stock, as production came back online.
Suppliers across Asia, starting in China, ramped up manufacturing and products started to flow again and the volumes were much bigger than before. Many of them PPE related and totally unplanned as governments bought stock in the early phases of the Covid pandemic.
Before long, with all the passenger aircraft grounded, the shipping lines were employing all their fleets and every container ship that could be bought or hired was put to work moving cargo across the oceans.
However, ports were built to handle relatively consistent volumes and each port is constrained by the number of cranes that can service ships and the available space to store containers.
When the ports became flooded with cargo, they simply didn’t have the capacity to handle it and the lack of labour, trucks, storage capacity and rail infrastructure all started to create significant supply chain challenges as congestion worsened.
Once a cargo shipment reaches the arrival port, it may go from truck to rail to warehouse to truck to distribution centre and any number of sorting facilities before it reaches a store or eCommerce customer. Many of the capacity constraints have been labour-related, i.e. COVID-safe working restricts port worker volumes, quarantine means under strength shifts at the distribution centres or simply not enough HGV drivers. Some of these issues are taking time to resolve, or may never be resolved.
Will the supply chain issues end soon? Very unlikely
Even if we can resolve bottlenecks, congestion and disruption to meet the current demand on the oceans, at the ports and in the trucks, any further significant increase in demand could undo any progress.
Businesses that don’t soon have enough inventory on hand are going to sell out prior to Christmas because lead times are so extended. We may see, after Lunar New Year, a very strong focus on inventory replenishment and with inventory-to-sales ratios so low, restocking may continue through the second quarter into the summertime and maybe all the way up to the peak season next year.
So, even if demand for services returns, we have a long way to go before the market catches up with anticipated demand. New vessel orders will not start to arrive until next year and will not add any significant volume before 2023-24 and, likewise, any infrastructure investments by ports or other participants, will take 12-36 months to plan and execute.Â
It is anticipated and widely accepted that the issues we see currently within the logistics sector and the high freight rates across all modes will continue next year without much compromise until the second half – hopefully.
Managing supply chains can no longer be a back-office function, largely ignored and taken for granted. More than ever, business survival will require a highly functioning supply chain run by professionals with the experience and critical support of partners.Â
Metro will always provide you with the alternatives and options available in the current market surrounded by proactive value added services, technology, communication and an overall solution throughout your own supply chains that is designed and created on a bespoke basis.
We encourage engagement and a collaborative partnership approach with all of our customers, and suppliers for that matter. For further information and to discuss your ongoing requirements please contact Elliot Carlile or Grant Liddell and let us visit you and demonstrate what we do and how we do it…….